
Project Description
To make this ceramic object was a multi-step process that used the CAD program Rhino to model, a 3D printer to print a physical model, plaster to make the mold which finally was used to slip cast the final ceramic vessel.
Concept Description
For my vessel I wanted to create a shape and pattern that would be difficult to recreate by wheel throwing or handbuidling, in addition to echoing the concept of my desk object from the previous project which utilzed organic curves into a pattern. T created a profile that was flattering to these wavy, repeating lines.

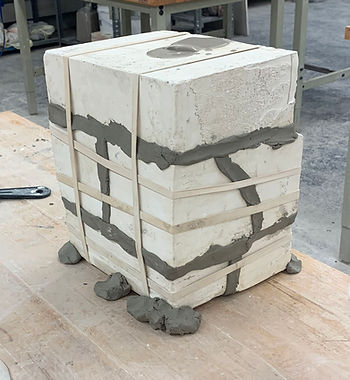
Prototyping Description
Once the object was modelled in Rhino and and 3D printed, parting lines were created to define each of the 8 part mold, including a top and bottom spare piece. These pieces are important to contain the slip that will be poured and to have an opening at the top of the vessel. Each part of the mold was sanded and banded together. The first pour failed, as there where spaces in between the mold parts. So, clay was used to fill in any and all spaces to prevent spilling once it was ready for the pour.


Outcome Description
The final output was this ovular-shaped vessel pictured on the top right of the four images. These images compare the bisqued vessel to the final glazed form. This drinking object was glazed using a satin matte glaze colored with 4% of sky blue.
Drinking Vessel (2019)
Ceramic
6" x 2.5" x 9"